Schiuma PIR come CORNER PROTECTION delle cisterne LNG
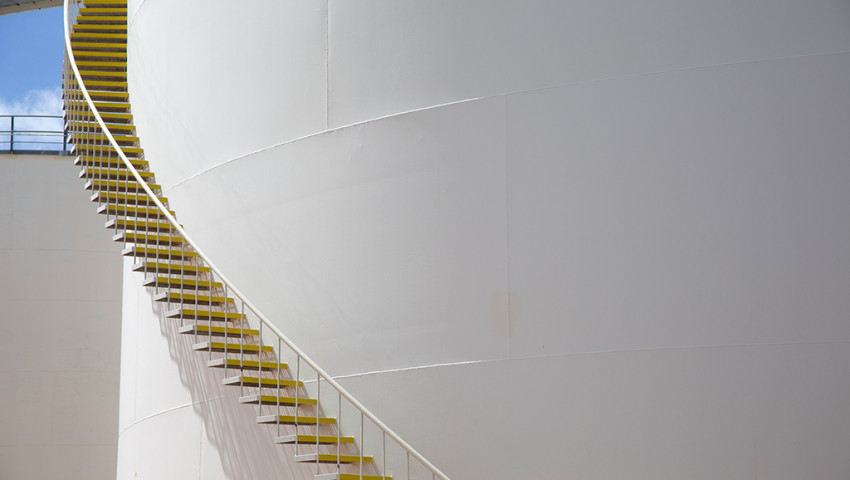
21.11.2013
A quasi 50 anni dalla messa in funzione del primo impianto LNG al mondo (Arzew GL4Z – Algeria 1964), è possibile fare delle considerazioni significative sull’evoluzione tecnologica che ha accompagnato la presa di coscienza e di ruolo dell'LNG come valida alternativa alle fonti energetiche tradizionali (in primis il petrolio), a partire dalla “taglia” degli impianti di produzione che è andata via via aumentando fino ad arrivare alla definizione di “jumbo Train” introdotta in Qatar a partire dal 2000.
La fortissima crescita della produzione, favorita dalle fondamentali scelte strategiche di Qatar, Indonesia e Australia, che hanno massicciamente investito in nuovi impianti a partire dagli inizi degli anni 2000, ha determinato una sempre maggiore disponibilità di LNG nel mercato dell’energia mondiale spingendo in parallelo la corsa al miglioramento delle tecnologie legate a questo prodotto sia in fase di produzione che di destinazione d’uso.
La ricerca si è concentrata in particolare sui vari processi dell’impianto di liquefazione per aumentarne la produttività e sui materiali che assicurano la buona efficienza di un impianto criogenico, in particolare gli isolanti.
Lavorare costantemente ad una temperatura di -162°C è stato fin dall’inizio una potente discriminante che ha escluso intere classi di materiali tradizionalmente utilizzati e che ha reso il processo di scelta della coibentazione molto selettivo in favore di materiali tecnici ad alte prestazioni.
La necessità di operare sempre più spesso su sistemi modulari, costruiti su spazi contingentati con modalità simili a quelle delle piattaforme offshore, ha ulteriormente enfatizzato la selezione degli isolanti ad elevate prestazioni spingendo al massimo la tecnicizzazione di un aspetto (l’isolamento appunto) in passato un po’ sottovalutato.
Da sempre nel settore dei materiali che mantengono il “freddo”, DUNA è stata fin da subito coinvolta nel processo di miglioramento delle specifiche degli impianti quando le principali società di ingegneria hanno iniziato a valutare l’opportunità di utilizzare schiume poliuretaniche (PUF) e poliisocianuratiche (PIR) al posto dei tradizionali materiali isolanti inorganici già noti (lane minerali, perlite, vetro cellulare, etc.).
Abbiamo quindi assistito direttamente alla progressiva analisi critica e successiva rivisitazione dei vari aspetti degli impianti in particolare, impianto di liquefazione, jetty lines e serbatoi.
Mentre i primi 2 aspetti sono stati affrontati fin da subito arrivando in poco tempo a risultati di grande valore tecnologico (su tutte il pre-isolamento delle Jetty lines effettuato per colata e spruzzo di sistemi PIR), per quanto riguarda i serbatoi di stoccaggio, la ricerca di soluzioni migliorative è incominciata nei primi anni 2000 ed è tuttora in corso.
Il serbatoio tradizionale (Land storage tank) a doppia parete è tipicamente isolato con vetro cellulare sul fondo e con perlite nell’intercapedine tra le due pareti; questa intercapedine può misurare fino a 1000 mm. Un ulteriore ring di vetro cellulare viene applicato sulla parete esterna della cisterna a partire dal fondo per un’altezza fino a 5 metri con uno spessore di circa 150-200 mm. Questo isolante, successivamente rivestito con cladding metallico, serve a costituire un contenimento in caso di perdite nel serbatoio in modo da avere il tempo necessario per mettere in sicurezza l’impianto (svuotamento rapido).
Il layout di questo tipo di serbatoi è rimasto sostanzialmente invariato fino all’inizio del 2000, quando teams di ingegneri hanno cominciato ad analizzare la tecnologia, mai messa in discussione prima in quanto funzionante e affidabile, con il fine di renderla più conveniente ed efficiente.
I materiali utilizzati, infatti, in particolar modo il vetro cellulare, per quanto funzionali, sono in effetti meno performanti dal punto di vista dell’isolamento rispetto ad altri tipi di prodotti già massicciamente utilizzati sulle linee fredde. In particolare le schiume poliuretaniche, supportate da rivestimenti protettivi sempre più tecnici, hanno progressivamente sostituito gli isolanti inorganici offrendo prestazioni migliori con ingombri (spessori di isolamento) e costi decisamente inferiori.
Cambiare il design di un sistema già funzionante non è per niente facile quindi i primi passi sono stati fatti lasciando invariati i disegni e procedendo a sostituire gradualmente i materiali. Grazie quindi alla collaborazione con DUNA nel 2002 la prima variante di un Land storage tank è andata on stream.
A seguito di una intensa campagna di test e di prove full scale la prima cisterna LNG con corner protection in PIR è stata quindi progettata e messa in opera.
L’impianto “pioniere” è stato quello del Sines in Portogallo per il quale DUNA ha fornito il CORAFOAM® bassa densità in pannelli preformati pronti per la messa in opera, nonché l’adesivo poliuretanico bicomponente DUNAMIX™ per il fissaggio dei pannelli alla parete della cisterna.
Rivestito nei punti critici, in corrispondenza dei punti di saldatura, con un tessuto di fibra ceramica, il PIR è stato successivamente rivestito con cladding metallico ad ottenimento di una corner protection formalmente equivalente alla precedente ma con il grande beneficio di un migliore isolamento e quindi maggiore efficienza e tenuta del contenimento del leakage.
La sostituzione del materiale è stata effettuata senza modificare le dimensioni della protezione; nonostante questo, il risparmio dell’operazione è stato dell’ordine del 50%.
Su un serbatoio anche di grandi dimensioni il corner protection non incide significativamente come costo; tuttavia, il buon esito dell’operazione ha aperto la strada ad un’analisi approfondita di tutto l’impianto, incluso il fondo della cisterna dove il vetro cellulare, pur performando egregiamente, non si è dimostrato molto versatile in termini di miglioramento delle performance rimanendo sostanzialmente uguale nel tempo.
Le schiume poliuretaniche invece essendo estremamente versatili sia da sole che legate con fibre minerali a formare compositi sembra essere l’elemento di forza per una rivoluzione della tecnologia di contenimento del LNG soprattutto in vista delle nuove destinazioni d’uso in studio.
Una particolare attenzione va soprattutto a due classi di nuove applicazioni di LNG: il bunkering, cioè l’utilizzo di LNG come fuel su grandi navi (cruise ships, container ships, etc.) e di conseguenza la costruzione di piccoli impianti di stoccaggio lungo le coste per rifornire queste flotte di navi “green” a basse emissioni.
Si tratterà quindi di costruire serbatoi di piccola taglia (miniaturizzazione) per ridurre l’impatto ambientale e renderli super efficienti. Di nuovo quindi l’isolamento sarà al centro dell’attenzione e DUNA sta già studiando soluzioni di supporto alla rivoluzione tecnologica in corso.
A seguito del progetto del Sines, molti altri progetti hanno visto l’utilizzo del PIR per il corner protection, questi i principali:
- Gate LNG (Olanda)
- Reganosa LNG e Huelva LNG (Spagna)
- Snøvit LNG (Norvegia)
- Skikda LNG (Algeria)